AN EXTENSION OF YOUR DESIGN TEAM
Morgan Polymer Seals is more than just a manufacturer. We’re a trusted part of your design team. Our design engineers work closely with you during each stage of the development process to create quality gaskets and seals, customized for your application. Because quality manufacturing starts with quality design.
Decades of Design Experience
Since 1997, we’ve manufactured thousands of custom seals for automotive OEMs around the world. We can help you create a new seal design from “scratch,” or leverage previous work to build your custom part.
Validated Designs Before Production
Our product designers perform comprehensive Finite Element Analysis (FEA) reports, which save countless hours and dollars by validating designs before production.
Tool Development & Product Testing
Our steel molds are sourced from US manufacturers and our product testing methods help ensure each seal can withstand the extreme environment of its application.
WHITE PAPER
Rubber Injection Molding
What's the best way to mold a rubber gasket? In this white paper, we compare the benefits of each molding process and outline best practices for quality manufacturing with rubber injection molding.
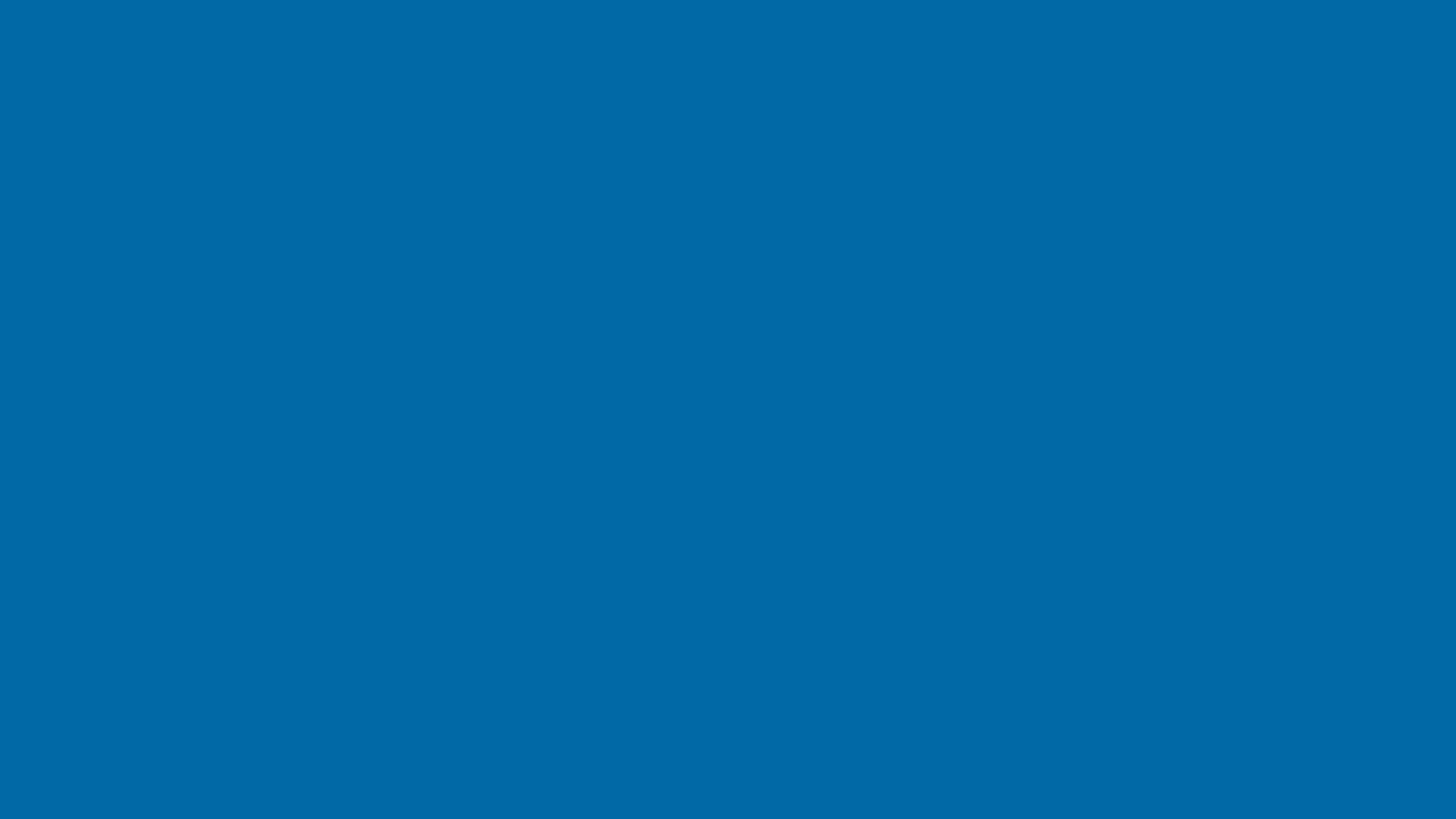
The Morgan Polymer Seal Design Process
Since 1997, Morgan Polymer Seals has supported the design of hundreds of sealing applications through our proven iterative development process. Our 8-stage process of design, testing, and analysis helps to ensure the quality and performance of your gasket through critical consideration of real-world forces.
BLOG
SUCCESSFUL SEAL DESIGN: WHAT'S THE PROCESS? (AND HOW LONG DOES IT TAKE?)
Environmental and application conditions impact the chemical mix of rubber composites and small changes to the complex blend of rubber materials significantly affect the way a product is manufactured. To design a rubber product that anticipates the effects of these small changes, experienced designers leverage advanced analysis and specialized requirements to find an optimal design for each application. Read our blog “Successful Seal Design: What's The Process? (And How Long Does It Take?)” to learn about Morgan Polymer’s proven seal design process.
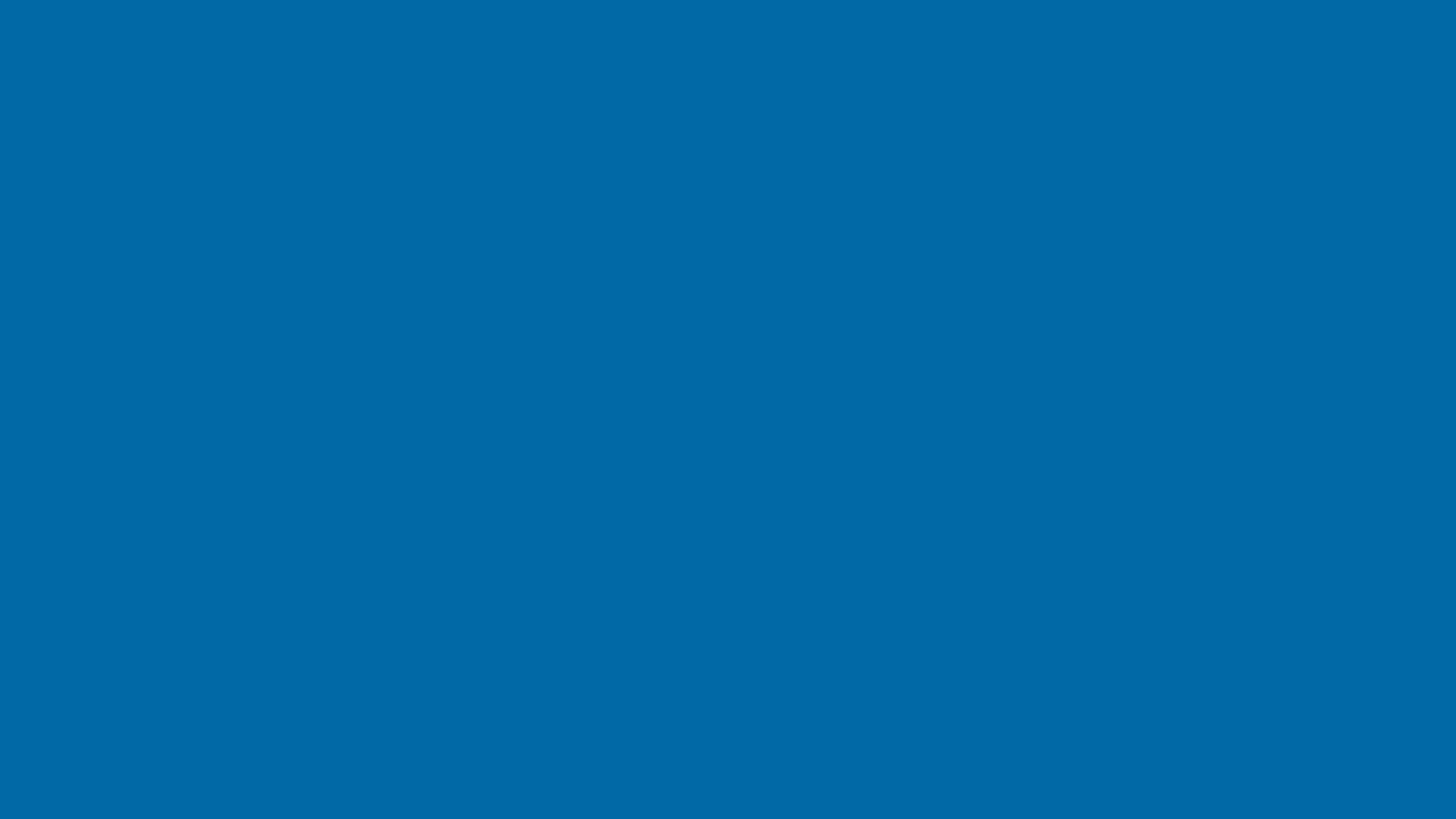
Capless Refueling for the Cadillac CT6
CASE STUDY
Capless refueling is an automobile design innovation that has saved millions in warranty claims for OEMs. These systems allow drivers to easily fill up their cars, while also offering improved safety and a reduced environmental impact of carbon emissions. Learn how we designed a mechanical seal for GM’s Cadillac CT6 capless refueling system that met existing size constraints and unique operational requirements.
BLOG
Successful Seal Design:FEA to Validate Your Design
Ever wondered how gasket designers can predict if their design will withstand the extreme environment of the seal's application?
At Morgan Polymer, our engineers perform Finite Element Analysis (FEA) to simulate how each gasket reacts to real-world conditions such as temperature, pressure, and displacements - and our FEA reports save customers time and money by validating a product's design before production begins. Read our blog post to learn how it's done.
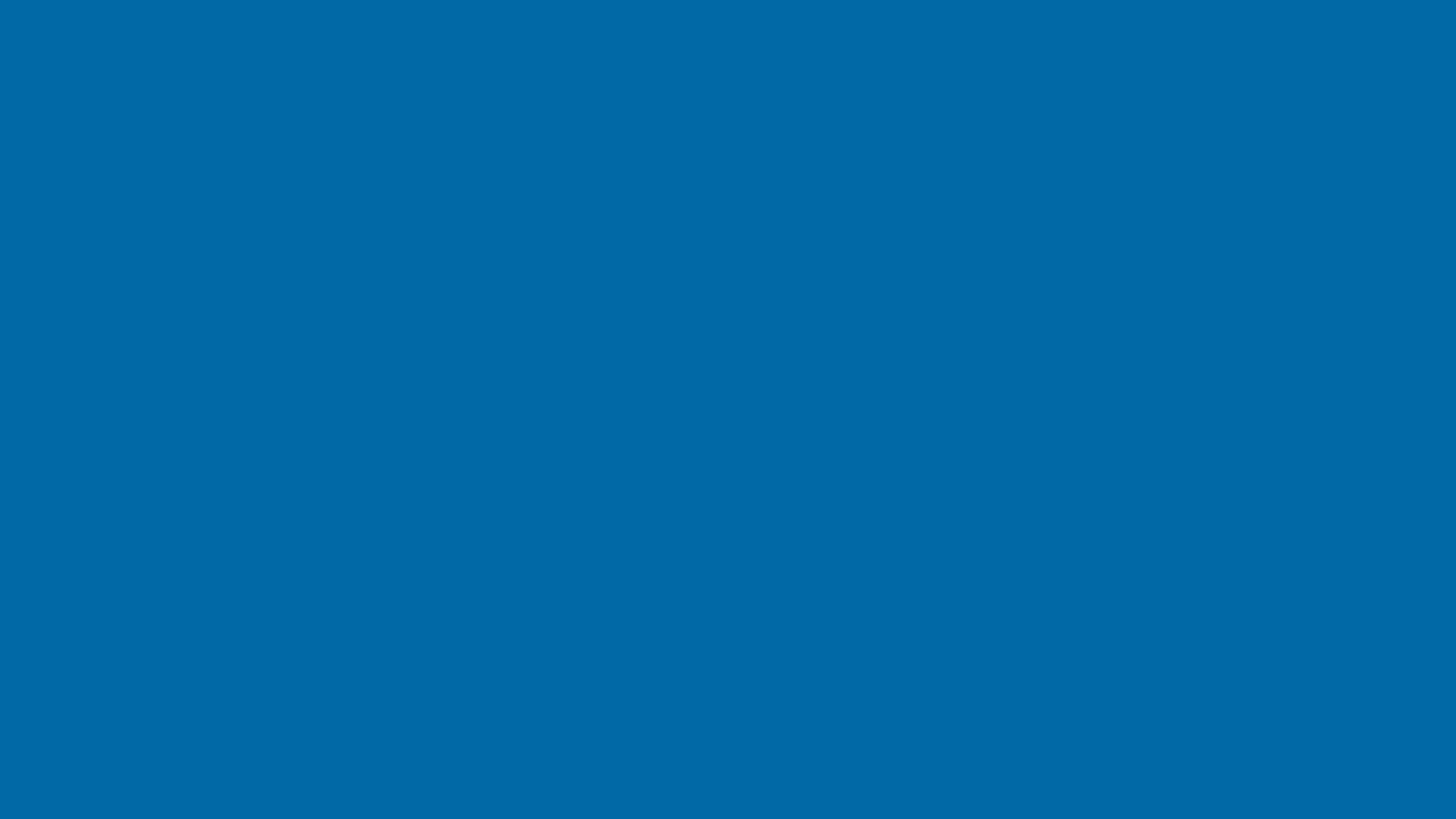
Contact Morgan Polymer Seals today to get started on your gasket design.
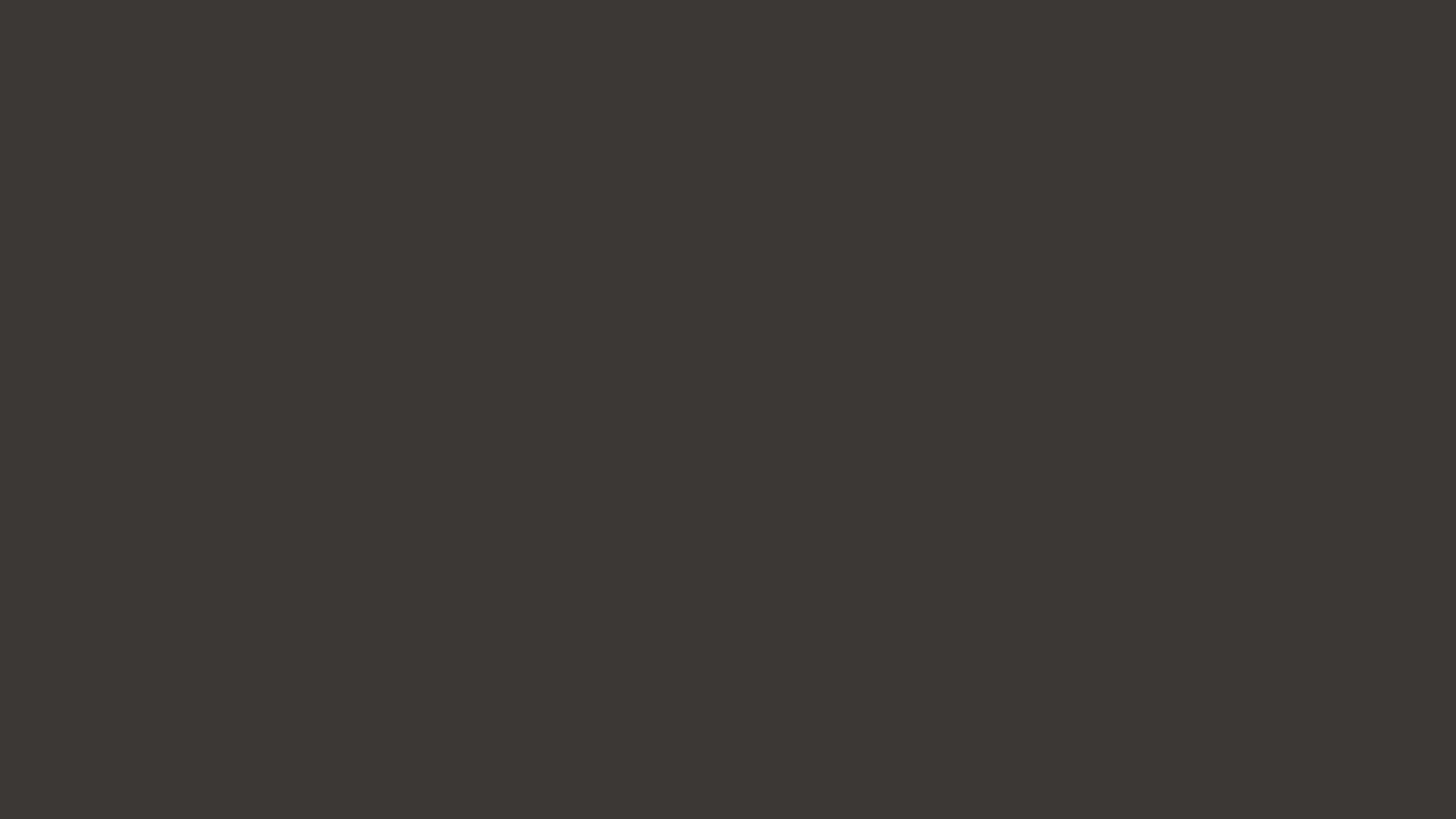